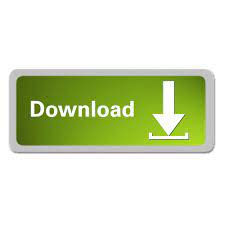
These stresses are the root cause of many quality issues in castings, such as distortion, cracking, or reduced lifetime during operation.Ĭasting stresses are changed significantly during the manufacturing process. Using knowledge about thermally induced casting stresses in design and manufacturing is gaining acceptance in industry. As an added benefit, the yield and tensile strengths of the components were tested and through these changes the mechanical properties were increased by around 10 %. Both factors taken together mean a reduction in cycle time about 20 s. The higher yield means a faster filling time, and thinner walls lead to a shorter solidification time. Through the new leaner runner bar, the yield is improved by around 18.5%. The improved gating system shows little turbulence during filling, the hotspot and shrinkage problem in the bottom of the casting are also eliminated. Several types of gating systems were simulated to analyze and solve these problems. In addition, the yield was only about 49 %. The filling pattern also led to a hotspot and a shrinkage defect in the bottom of the casting. The top ingate was filled too quickly, and this caused casting defects due to turbulence and a large amount of entrapped air. The original design of the gating system of the front fork led to several problems that were detected by simulation. The original gating system of a front fork component led to problems that were analyzed using MAGMASOFT ®. This approach leads to an optimized design and casting process of the engine block. To avoid problems, a manufacturing process simulation can be performed at an early stage of the design process, where geometric or casting process modifications may be made to decrease the level of tensile stresses. The biggest influences on residual stresses in castings are the design (80%) and the casting process itself (20%). One can try to use compressive stresses as a pre-loading, like in pre-tensioned concrete. It is unusual that compressive stresses are critical. Nevertheless, even if tensile stresses are below the critical value, the casting may fail during assembly, or even worse during driving.Ĭompressive stresses are the opposite of tensile stresses and are those stresses that are induced by pushing. As a rule, tensile residual stresses are lower than this threshold value and the casting does not fail during the casting process. By reaching this value, cracking occurs and the part fails. Tensile stresses, those stresses that are induced by “pulling”, may be critical during the manufacturing process, if their value exceeds the material’s tensile strength. Residual stresses develop during solidification and cooling of the casting due to uneven cooling rates in the different wall thicknesses. Only by using manufacturing process simulation, is it possible to determine the distribution of residual stresses in castings and to consider these properties in the design optimization process. Their performance and weight are, among other criteria, dependent on their geometry and the casting process, especially defects like porosity and residual stresses. Every learning circle is new learning content with a new set of peers.Cast iron engine blocks can be found in more than half of all passenger cars.
#Magmasoft tech levels series
The Renshu-Kenshu learning circle series emphasizes learning by doing, facilitated learning (not training), collective learning and digital literacy. Renshu-Kenshu in the Japanese language means Practice-Training.
#Magmasoft tech levels free
There are many advantages to enjoy and here are just three (1) Singapore-based accredited teacher-facilitators (2) learning at our own time and at our own pace (3) collectively learning with our peers (4) no evaluation, free to evolve (5) progression and appreciation The facilitators jump in to help us all progress to the next level. We all take moments now and then to appreciate as well as curate the learning from each other. But, there are no fixed times, you choose the time to engage. Too much focus on perfection versus progressionĪ learning circle is facilitated for four weeks in a month, three days a week (T, W, Th) and 30-45 minutes a day. Constrained by the teachers, system and time (respectfully)
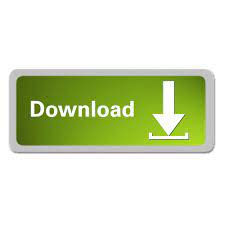